domingo, 15 de abril de 2012
El B-52 cumple 60 años
El B-52 cumple 60 años:
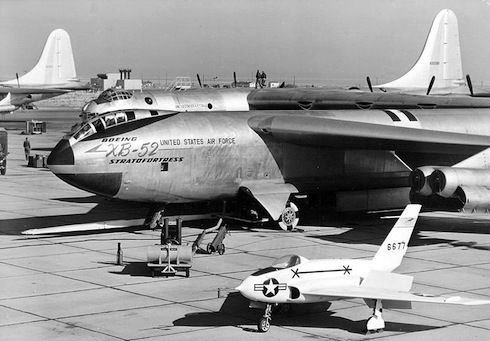
Hoy, el archifamoso B-52 está de cumpleaños. Un 15 de abril de 1952 el piloto de pruebas Alvin "Tex" Jonhson hacía volar por primera vez el XB-52.Sesenta años después, sabemos que seguirá volando durante MUCHO tiempo, siendo sin duda el avión más longevo en servicio activo.
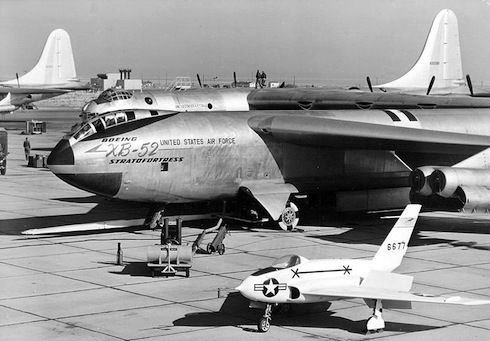
Hoy, el archifamoso B-52 está de cumpleaños. Un 15 de abril de 1952 el piloto de pruebas Alvin "Tex" Jonhson hacía volar por primera vez el XB-52.Sesenta años después, sabemos que seguirá volando durante MUCHO tiempo, siendo sin duda el avión más longevo en servicio activo.
Latest Apache Helicopter Controls Unmanned Aircraft - Aviation International News
Latest Apache Helicopter Controls Unmanned Aircraft - Aviation International News:
![]() Aviation International News | Latest Apache Helicopter Controls Unmanned Aircraft Aviation International News (Photo: Bill Carey) US Army AH-64D Block III helicopter crews exercised directional control of the MQ-1C Grey Eagle unmanned aircraft system (UAS) during the recently completed initial operational test and evaluation (IOT&E) of the upgraded Apache. |
Defensa descarta Trasmiras como base aérea de la OTAN - La Región Internacional
Defensa descarta Trasmiras como base aérea de la OTAN - La Región Internacional
El ministro de Defensa, Pedro Morenés, confirmó de forma indirecta que Trasmiras no va a albergar un centro para aviones no tripulados y, menos aún, será la sede del sistema de vigilancia terrestre conocido por sus siglas en inglés AGS (Alliance Ground Surveillance). Morenés explicó esta semana en una entrevista radiofónica que España se va a reincorporar de forma inmediata al proyecto AGS que la OTAN quiere poner en marcha en 2015 y cuyo principal objetivo es el desarrollo de aviones no tripulados ?conocidos como drones? para operar en zonas en conflicto sin riesgo para las vidas humanas.
El ministro de Defensa, Pedro Morenés, confirmó de forma indirecta que Trasmiras no va a albergar un centro para aviones no tripulados y, menos aún, será la sede del sistema de vigilancia terrestre conocido por sus siglas en inglés AGS (Alliance Ground Surveillance). Morenés explicó esta semana en una entrevista radiofónica que España se va a reincorporar de forma inmediata al proyecto AGS que la OTAN quiere poner en marcha en 2015 y cuyo principal objetivo es el desarrollo de aviones no tripulados ?conocidos como drones? para operar en zonas en conflicto sin riesgo para las vidas humanas.
Fuerza Aérea de EEUU convoca a Embraer y Hawker a nueva licitación - Univisión
Fuerza Aérea de EEUU convoca a Embraer y Hawker a nueva licitación - Univisión:
Fuerza Aérea de EEUU convoca a Embraer y Hawker a nueva licitación Univisión La Fuerza Aérea estadounidense anunció este viernes que convocará a la empresa aeronáutica brasileña Embraer ya la estadounidense Hawker Beechcraft a una nueva licitación para la compra de aviones ligeros con destino Afganistán a partir del 17 de abril ... y más » |
Tecnam confirmed that it will offer the Rotax 912 iS (injection) engine into new build aeroplanes from as early as Summer 2012.
Tecnam outlines plans to incorporate the recently launched Rotax 912 iS engine offering into its extensive range of aeroplanes
Tecnam today confirmed that it will offer the Rotax 912 iS (injection) engine into new build aeroplanes from as early as Summer 2012.
With the Rotax 912 iS engine potentially delivering significantly better fuel efficiency than comparable competitive engines in the light sport, ultra-light aircraft and the general aviation industry. Tecnam announced today that it will offer the Rotax 912 iS engine to all Advanced Ultralight (AUL) and Light Sport Aircraft (LSA) customers whose aeroplanes deliver after July 2012.
Rotax have incorporated technology enhancements such as a modern fuel injection system and digital engine control unit (ECU) to the Rotax 912 iS engine to ensure optimal fuel and air mixture at any altitude for longer flight range, lower operating costs and CO2 emission reduction.
The development of a 4-stroke, 4-cylinder 100 hp aircraft engine with a redundant electronic fuel injection system is a first in the industry
The injection system ensures the best fuel and air mixture on each cylinder at every possible altitude while delivering the same 100 hp as the Rotax 912 ULS engine,
therefore producing fewer emissions.
The new Rotax 912 iS engine also provides a time of 2,000 hours between overhauls (TBO); the same TBO as the 912 engine.
“Once Rotax have achieved EASA certification, Tecnam will commence work on a ‘major change’ for the entire Tecnam range of aeroplanes” said Paolo Pascale, Tecnam’s Managing Director. “To our customers this should reduce the fuel cost (be it Mogas or Avgas) between 20% and 40%!”
Rotax anticipate final EASA certification of the 912 iS this June for certified aircraft in CS/VLA, CS23 and FAR 23 categories.
Tecnam today confirmed that it will offer the Rotax 912 iS (injection) engine into new build aeroplanes from as early as Summer 2012.
With the Rotax 912 iS engine potentially delivering significantly better fuel efficiency than comparable competitive engines in the light sport, ultra-light aircraft and the general aviation industry. Tecnam announced today that it will offer the Rotax 912 iS engine to all Advanced Ultralight (AUL) and Light Sport Aircraft (LSA) customers whose aeroplanes deliver after July 2012.
Rotax have incorporated technology enhancements such as a modern fuel injection system and digital engine control unit (ECU) to the Rotax 912 iS engine to ensure optimal fuel and air mixture at any altitude for longer flight range, lower operating costs and CO2 emission reduction.
The development of a 4-stroke, 4-cylinder 100 hp aircraft engine with a redundant electronic fuel injection system is a first in the industry
The injection system ensures the best fuel and air mixture on each cylinder at every possible altitude while delivering the same 100 hp as the Rotax 912 ULS engine,
therefore producing fewer emissions.
The new Rotax 912 iS engine also provides a time of 2,000 hours between overhauls (TBO); the same TBO as the 912 engine.
“Once Rotax have achieved EASA certification, Tecnam will commence work on a ‘major change’ for the entire Tecnam range of aeroplanes” said Paolo Pascale, Tecnam’s Managing Director. “To our customers this should reduce the fuel cost (be it Mogas or Avgas) between 20% and 40%!”
Rotax anticipate final EASA certification of the 912 iS this June for certified aircraft in CS/VLA, CS23 and FAR 23 categories.
Tecnam's four seater P Twenty-Ten took to the skies for the first time today
Under the control of Tecnam’s Test Pilot, Marco Locatelli, Tecnam’s all new P Twenty-Ten achieved a faultless first flight at 16.42 UTC, over the skies of Tecnam’s Capua production facility. Marco Locatelli’s test flight report included the following details.
Aircraft mass was 900kg. Lycoming IO-360 max power was attained with aircraft on the brake: 28,20 inHg MAP, 2680 RPM, no wind. After brake release normal engine behaviour and parameters were recorded and a slight increase in MAP (28,5 inHg) and prop speed (2690 RPM) was noticed. Aircraft acceleration to 50 KIAS took 8 seconds and about 300-350 ft. Effortless rotation and lift off occurred at approximately 60 KIAS.
At 5000 ft 80 KIAS flaps were retracted to UP. Two to three pitch attitude angle degrees increase was set with a progressive modest pull back effort. Indicated airspeed was promptly increasing towards. Engine was then reduced to 20 InHG, 2450 RPM and speed stabilized at 100 KIAS.
Pilot noted that level flight is easily kept once on trim, excellent outer view allows the pilot to have good horizon visual references and that the Garmin PFD provides superb attitude and situational awareness cues.
Longitudinal, lateral and directional static stability were clearly proven at 119 KIAS, 5000 ft.
A progressive levelled deceleration was initiated, 2-3 kts per second. It was possible to stop speed deceleration just by mean of pitch control, manual trim compensation was required since significant effort variation was recorded in the order of 6-8 daN per 20 KIAS of delta. Both lateral and direction controls keep effective and precise, rudder effort definitely lower, but never reversing.
After several canonical flight envelope opening tests were performed, including stalling, a TO flap and a LD flap go around passage were performed followed by a final landing on Capua’s runway 26.
From a 2,5 degrees approach path, LD flap approach at 65 KIAS runway touch down was obtained on the centerline at about 48 KIAS, 30 minutes after take off on Tecnam homebase field.
Marco went on to comment that the P Twenty Tens’ behaviour appears safe and predictable in all investigated speed initial envelope, flight controls are precise and effective, attitudes can be attained with a sufficient precision of 1-2 deg on all axis. Speed and flight controls displacement and effort curves are in the correct sense; pitch trim is (manually) usable and effective. This is a positive characteristic for a school initial trainer a/c, since it may provide very good airspeed delta feedback to student pilots.
The P Twenty Ten brings together an advanced technology all carbon fibre fuselage with a metal wing and stabilator based on the best of TECNAM’s recent P2006T Twin and P2008 offerings, this single engine, 4 seat aeroplane is eagerly anticipated by the General Aviation community.
Utilising both carbon fibre and metal has allowed Tecnam to optimise aerodynamic quality and reliability. Carbon fibre ensures smooth surfaces and allows for an elegance and styling you would expect from Italy. Metal is used for the wing and stabilator to provide further strength and stability.
Powered by a Lycoming IO-360-M1a (‘Lycoming Light’) engine, providing 180HP and 2700RPM. The wing is based on the well-proven NACA63A aerofoil. Through partial tapering, the design brings it close to the optimal lift distribution (elliptical).
The all movable type (stabilator) horizontal tail, a trade mark of all TECNAM aeroplanes, allows for excellent controllability and ‘hands off’ longitudinal stability.
The nose gear is free castering and consists of a tubular steel leg connected to the lower engine mount attachments and is braced by a rubber shock absorber. The landing gear is also faired to minimise drag, whilst ground steering is by differential braking.
The TECNAM P2010 has a high fuel capacity (210lt, 46.2 imp. gal). The fuel tanks are installed in the wing box, behind the main spar, to preserve their integrity in case of an accident. Of course carbon fibre equals a lighter and therefore more fuel efficient aeroplane.
Tecnam has always paid great attention to comfort for both pilots and passengers. The cabin width also allows for a large instrument panel, with its modular design specifically tailored to allow the customer to fit either an analogue or digital instrumentation package.
“It’s been an extraordinarily successful and exciting time for the Tecnam design, production and flight-test teams” said Paolo Pascale, Tecnam’s Managing Director. “The Tecnam P Twenty-Ten further exhibits our commitment to innovation, style and advanced technology and is yet another extension of our passion for flying. Our on-going sales success has resulted in Tecnam delivering a new aeroplane every working day”.
Aircraft mass was 900kg. Lycoming IO-360 max power was attained with aircraft on the brake: 28,20 inHg MAP, 2680 RPM, no wind. After brake release normal engine behaviour and parameters were recorded and a slight increase in MAP (28,5 inHg) and prop speed (2690 RPM) was noticed. Aircraft acceleration to 50 KIAS took 8 seconds and about 300-350 ft. Effortless rotation and lift off occurred at approximately 60 KIAS.
At 5000 ft 80 KIAS flaps were retracted to UP. Two to three pitch attitude angle degrees increase was set with a progressive modest pull back effort. Indicated airspeed was promptly increasing towards. Engine was then reduced to 20 InHG, 2450 RPM and speed stabilized at 100 KIAS.
Pilot noted that level flight is easily kept once on trim, excellent outer view allows the pilot to have good horizon visual references and that the Garmin PFD provides superb attitude and situational awareness cues.
Longitudinal, lateral and directional static stability were clearly proven at 119 KIAS, 5000 ft.
A progressive levelled deceleration was initiated, 2-3 kts per second. It was possible to stop speed deceleration just by mean of pitch control, manual trim compensation was required since significant effort variation was recorded in the order of 6-8 daN per 20 KIAS of delta. Both lateral and direction controls keep effective and precise, rudder effort definitely lower, but never reversing.
After several canonical flight envelope opening tests were performed, including stalling, a TO flap and a LD flap go around passage were performed followed by a final landing on Capua’s runway 26.
From a 2,5 degrees approach path, LD flap approach at 65 KIAS runway touch down was obtained on the centerline at about 48 KIAS, 30 minutes after take off on Tecnam homebase field.
Marco went on to comment that the P Twenty Tens’ behaviour appears safe and predictable in all investigated speed initial envelope, flight controls are precise and effective, attitudes can be attained with a sufficient precision of 1-2 deg on all axis. Speed and flight controls displacement and effort curves are in the correct sense; pitch trim is (manually) usable and effective. This is a positive characteristic for a school initial trainer a/c, since it may provide very good airspeed delta feedback to student pilots.
The P Twenty Ten brings together an advanced technology all carbon fibre fuselage with a metal wing and stabilator based on the best of TECNAM’s recent P2006T Twin and P2008 offerings, this single engine, 4 seat aeroplane is eagerly anticipated by the General Aviation community.
Utilising both carbon fibre and metal has allowed Tecnam to optimise aerodynamic quality and reliability. Carbon fibre ensures smooth surfaces and allows for an elegance and styling you would expect from Italy. Metal is used for the wing and stabilator to provide further strength and stability.
Powered by a Lycoming IO-360-M1a (‘Lycoming Light’) engine, providing 180HP and 2700RPM. The wing is based on the well-proven NACA63A aerofoil. Through partial tapering, the design brings it close to the optimal lift distribution (elliptical).
The all movable type (stabilator) horizontal tail, a trade mark of all TECNAM aeroplanes, allows for excellent controllability and ‘hands off’ longitudinal stability.
The nose gear is free castering and consists of a tubular steel leg connected to the lower engine mount attachments and is braced by a rubber shock absorber. The landing gear is also faired to minimise drag, whilst ground steering is by differential braking.
The TECNAM P2010 has a high fuel capacity (210lt, 46.2 imp. gal). The fuel tanks are installed in the wing box, behind the main spar, to preserve their integrity in case of an accident. Of course carbon fibre equals a lighter and therefore more fuel efficient aeroplane.
Tecnam has always paid great attention to comfort for both pilots and passengers. The cabin width also allows for a large instrument panel, with its modular design specifically tailored to allow the customer to fit either an analogue or digital instrumentation package.
“It’s been an extraordinarily successful and exciting time for the Tecnam design, production and flight-test teams” said Paolo Pascale, Tecnam’s Managing Director. “The Tecnam P Twenty-Ten further exhibits our commitment to innovation, style and advanced technology and is yet another extension of our passion for flying. Our on-going sales success has resulted in Tecnam delivering a new aeroplane every working day”.
Conferencia SAE: "AVANCES EN TECNOLOGÍA AERONÁUTICA: Desarrollos tecnológicos de Boeing en Europa"
| |||||||
| |||||||
| |||||||
Lockheed displays F-35 JSF cockpit demonstrator
Lockheed displays F-35 JSF cockpit demonstrator: Lockheed Martin has displayed its F-35 Lightning II Joint Strike Fighter (JSF) aircraft mobile cockpit demonstrator at the Northrop Grumman facility in California, US.